MMS allows monitoring and recording mechanized agricultural work in the fields in real time, comparing planned and actual indicators as well.
Machinery monitoring systems include:
- set of sensors
- coordinate determination unit with a mobile communication modem;
- controller-receiver of sensor values;
- ISOBUS bus;
- telematic server.
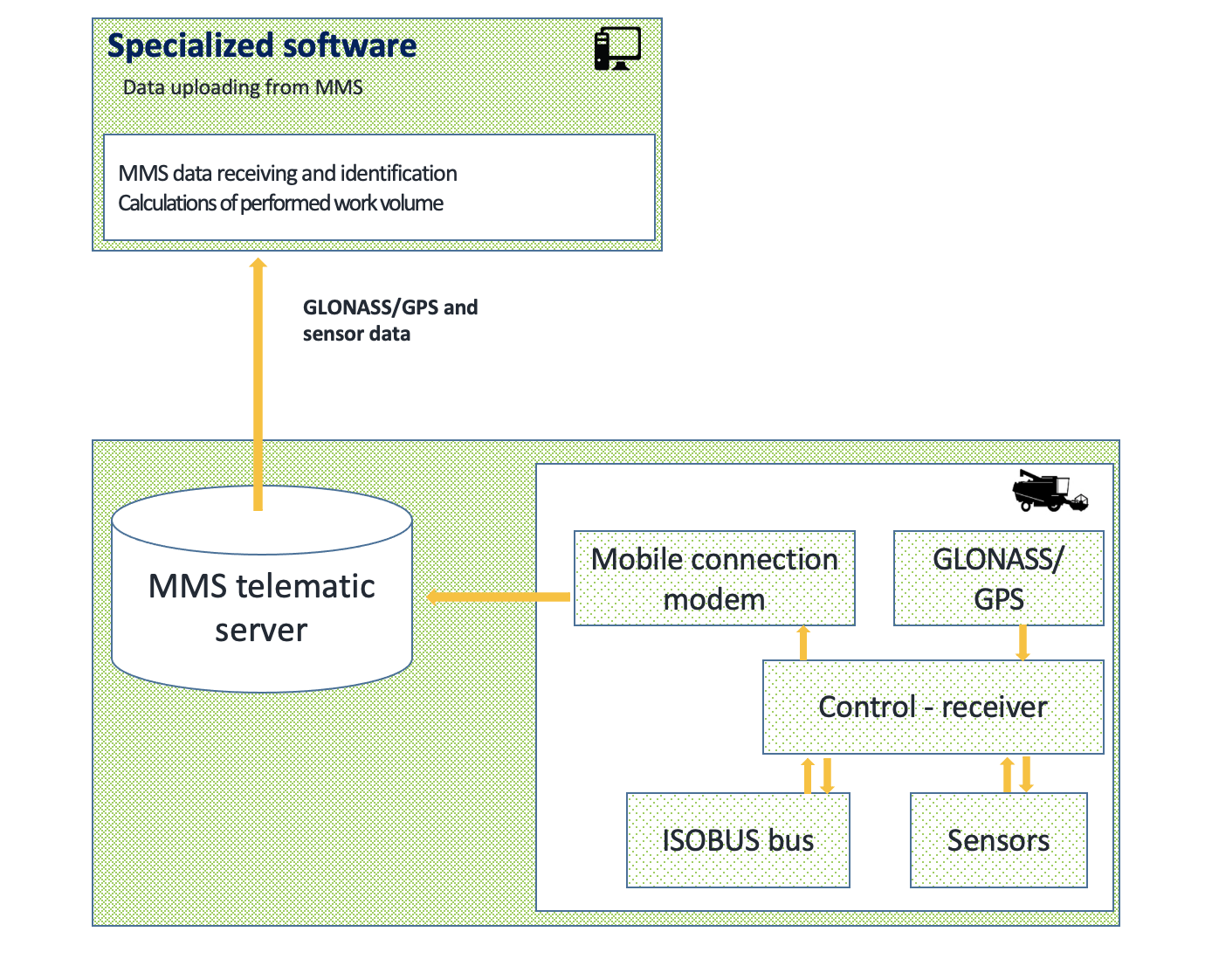
- fuel flow sensor;
- driver recognition sensor using RFID cards;
- electronic tags to identify implements.
There are also sensors that record functional operations: lifting the body, the bucket, turning on the harvester or the auger, seeding depth, etc. The operation principle of MMS is based on the control receiving information from the connected sensors and its subsequent transmission via mobile channels to the telematics server. The telematics server processes the incoming data and provides their storage. Another important function of the telematics server is to provide transmission of values and/or sensors’ parameters to an external system for subsequent data processing.
As there are a lot of diverse vehicle control systems there is a necessity for their unification and standardization. So, in the early 1990s, the Society of Automotive Engineers (SAE) subcommittee on control systems began developing an application profile based on the CAN fieldbus for the internal communication network of trucks. In 1998, SAE published a set of specifications - J1939, used to unite the controllers installed in trucks and trailers, and provide the communication between the engine, transmission, braking system.
Common J1939 communication functions have put to good use in the agricultural industry in the CAN application profile for agricultural and forestry machines ISO 11783 as well as the CAN application profile for trucks and trailers ISO 11992. The international standard ISO 11783 establishes a communication system for agricultural machinery based on the CAN 2.0B protocol (J1939 profile. The ISOBUS name is used for such standards now).
In 2001, agricultural machinery manufacturers agreed to introduce the ISO 11783 standard, which allowed common communication interfaces to be used in tractors, implements and control systems for agricultural machinery. This allows machinery from different manufacturers to communicate with each other, with fewer special control devices dedicated to specific fixtures, terminals and displays. One monitor in the tractor cab allows controlling all the implements - field baler, sprayer, spreader, seeder, etc. - and establishes communication with the tractor and the agricultural control system. The development of the ISO11783 standard is still not complete and is in the process at the moment.
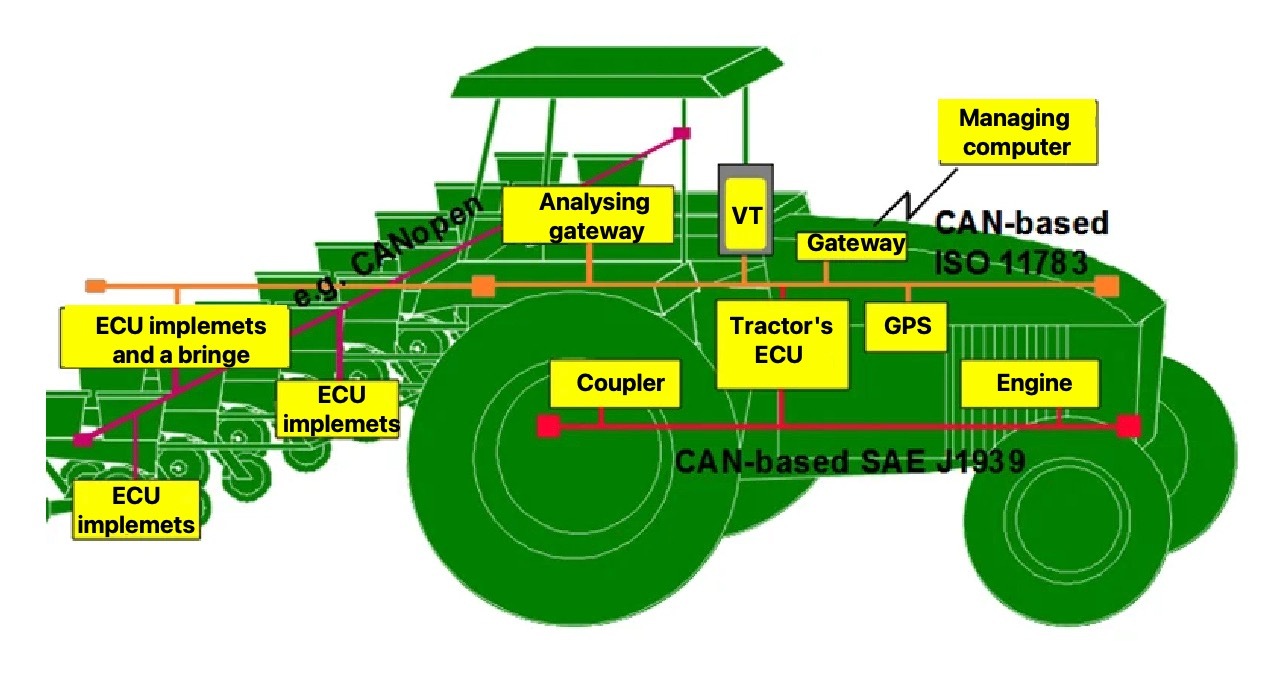
where
ECU - SAE J 1939 controller
VT - ISO 11783 virtual terminal.
Let us consider the influence of location and navigation systems for machinery on the accuracy of calculations for quantitative and qualitative accounting of agricultural work in production fields.
The study is about the influence of the accuracy of agricultural machinery coordinates on values such as mileage, cultivated area, speed, time, location, when using MMS .
Mileage:
MMS technology provides an error in calculating the mileage of no more than 1.4% for urban conditions and no more than 0.5% for open areas with a minimum number of visible satellites (4).
Cultivated area:
The accuracy of calculating the cultivated areas, taking the working width of the agricultural unit into account, depends on the accuracy of constructing the track of the machinery movement and on the accuracy of production field vector maps.
The machinery unit movement track visible on the map is a satellite antenna movement track. Therefore, it is important to choose the right location for the antenna installation.
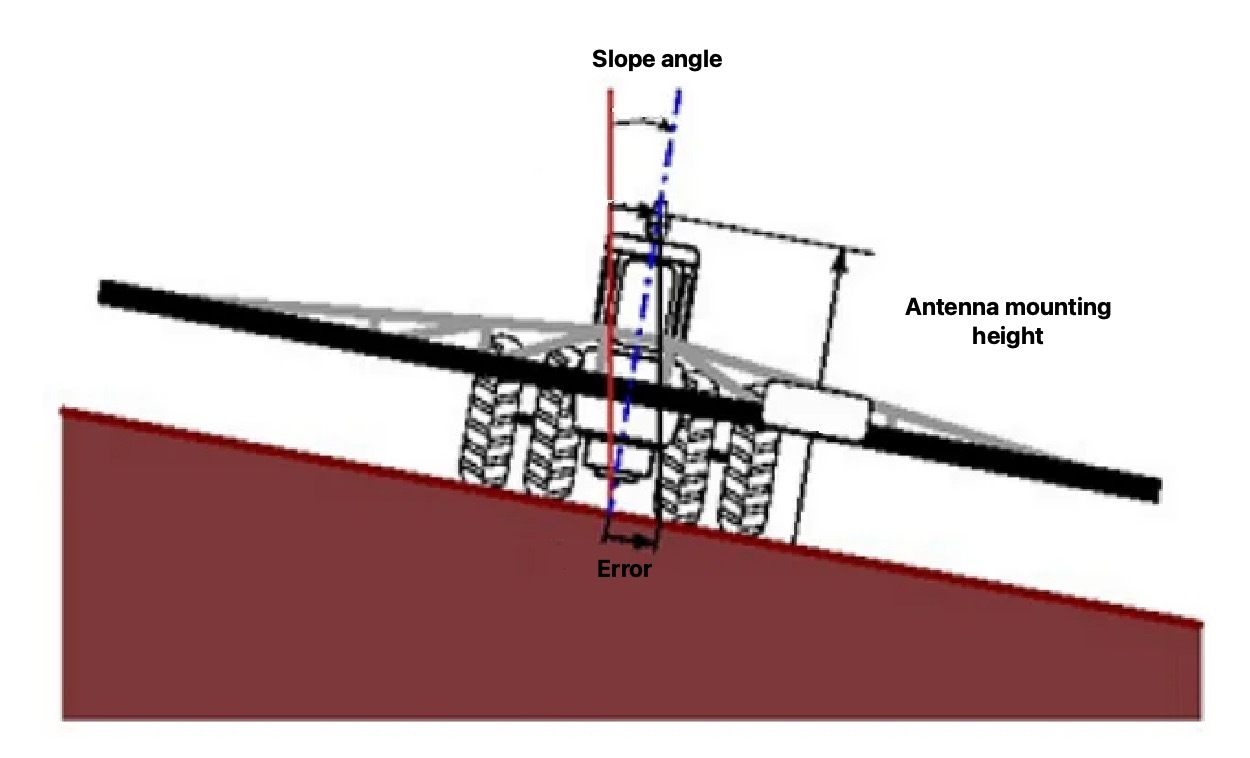
Since the GLONASS / GPS telematics terminals do not have slope compensators, when the slope is 10°, the deviation of the track can reach 1 meter, depending on the antenna installation height. The problem is sufficiently solved by installing a satellite antenna in front of the hood along the symmetry axis along the machinery unit. Also, such installation reduces the effect of electromagnetic radiation of on-board electronic equipment in the cab on the GLONASS / GPS highly sensitive receiving antenna.
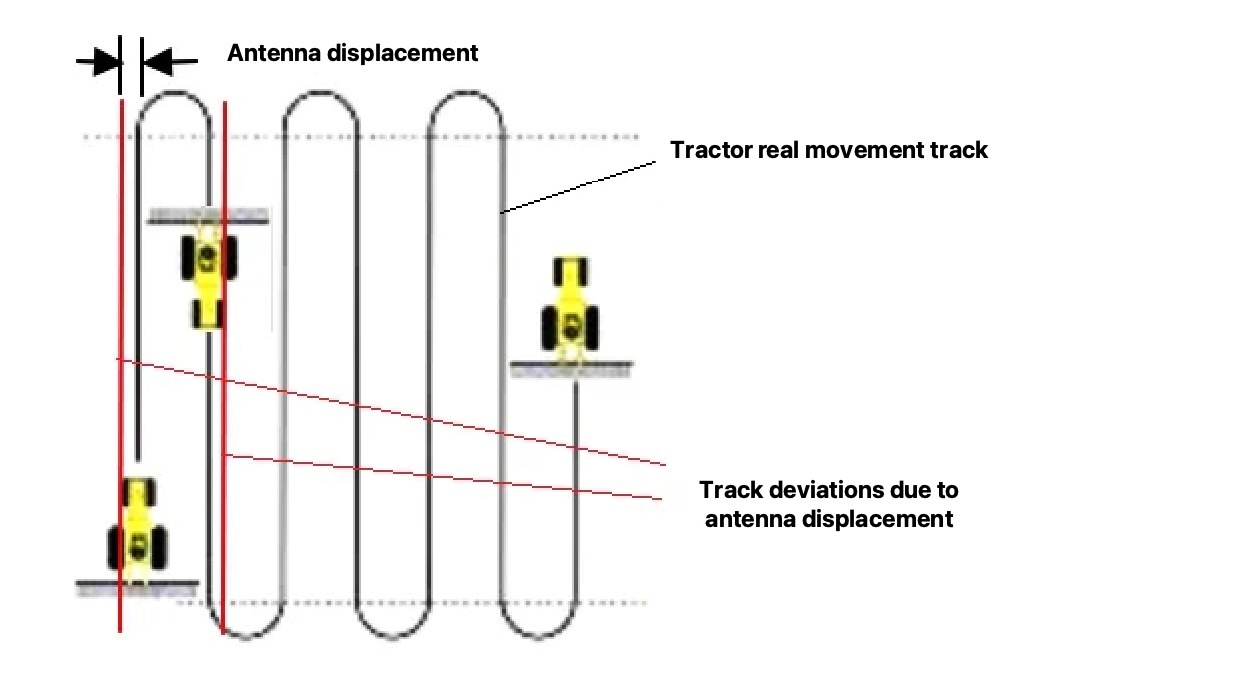
Installing a receiving satellite antenna on the cab roof, (not along the axis of symmetry) leads to a track dislocation. With a cab width of 1.5 meters, the dislocation is 0.75 meters. In this case, when the tractor moves in opposite directions, the track error will reach 1.5 meters. There can be gaps or overlaps, which in fact are not there, but it can affect the result of calculating the cultivated area.
Another significant factor in the accuracy of the processed area is the work quality and linking of electronic maps to the coordinate system used in GIS systems. Typical errors in the vectorization of maps, leading to inaccurate calculation of the processed areas and program failures, are incorrect vectorization of field contours, lack of unprocessed area marking in the fields, topology errors. These errors are illustrated in the figures below.
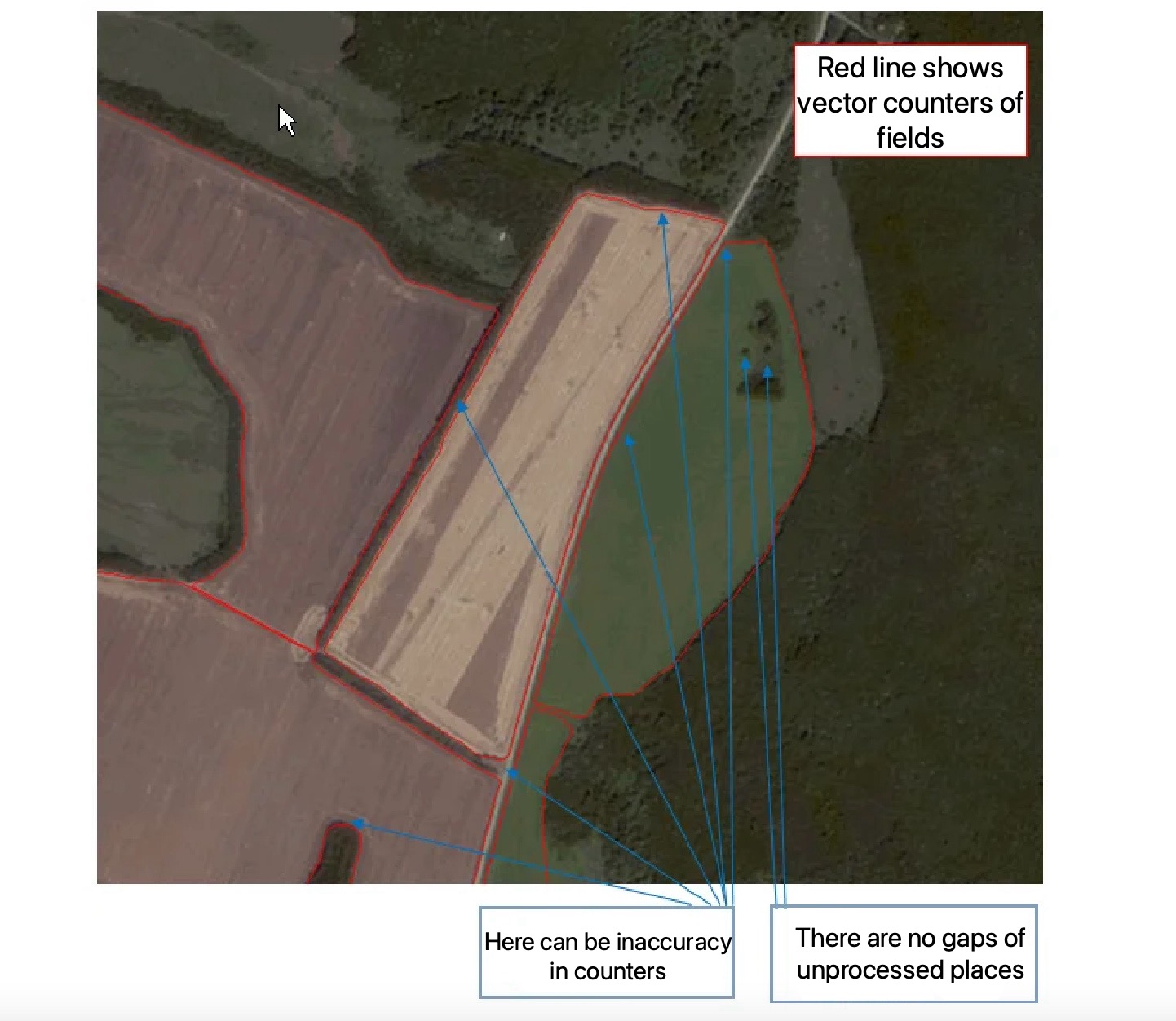
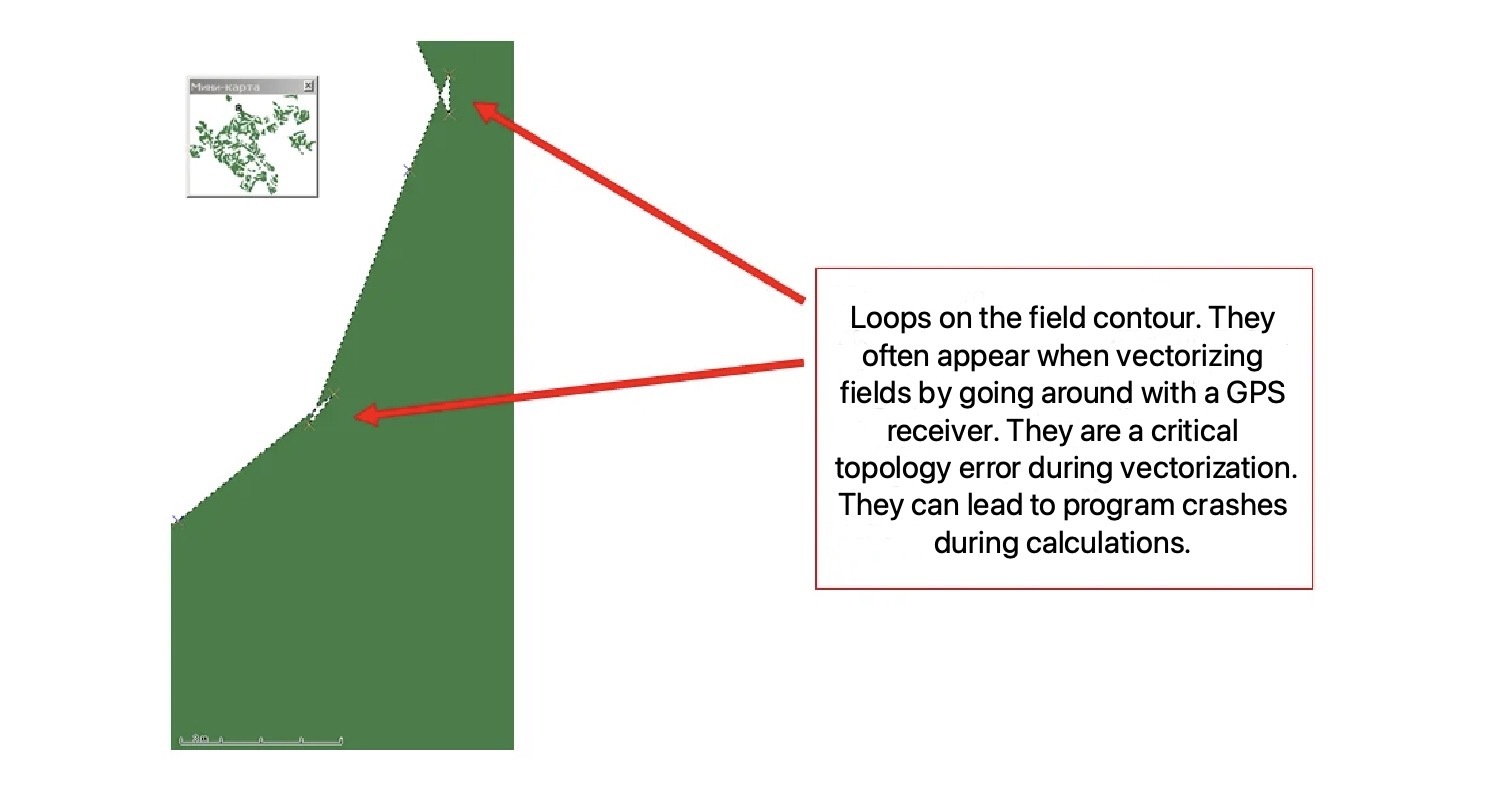
Speed:
In the MMS, the machinery unit speed is determined with the help of the GLONASS / GPS module by the Doppler effect (the frequency of the received signal depends on the radial speed of approaching to or distancing from the signal source - GLONASS / GPS space satellite systems). Accuracy may be lower with fewer available satellites. In MMS, the accuracy of speed determining is forcibly reduced to 0.1 km / h, since this is quite enough to ensure compliance with the requirements of the technology for performing agricultural work.
Time:
Accurate timing is a major requirement for satellite navigation equipment, since there is a propagation delay of radio signals from different satellites. For navigation tasks, the module determines the time with an error of no more than 340 nanoseconds. In this case, the time of GLONASS / GPS receivers are synchronized with the atomic one of spacecraft. In MMS, the time of all events is rounded off up to 1 second, as this is sufficient for making reports.
Location:
The average error in determining the machinery location using satellite technology is 2-6 meters. At present, the accuracy of the coordinates made by the GLONASS system corresponds to the equivalent indicators for GPS. According to the reports of the East-European System of Differential Correction and Monitoring, the errors of daily navigational sighting of GLONASS were 4.3-7,86 meters in longitude and latitude. The reports were generated according to the data from 22 stations of the GLONASS and GPS systems for monitoring the functioning quality of space navigation systems, as of July 18, 2016, when using 8-9 spacecraft (depending on the receiving point). At the same time, GPS errors were 3.72-7.29 meters when using 10-12 spacecraft (depending on the receiving point). Using both navigation systems together, the errors were 3.37-6.17 meters when using 18-21 spacecraft (depending on the location of the receiving point).
Navigation accuracy is determined by the number of satellites in the constellation used and their relative position. This, in its turn, depends on the width of the GLONASS / GPS antenna direction and its positioning (horizon view). The minimum error is achieved in open areas. A significant error (up to several hundred meters) can be observed for a short time when working in rooms or well courtyards (the influence of multiple reflected signals), under power lines, near forest plantations, and in cases when the GLONASS / GPS receiver was just turned on and did not have time to identify all visible satellites. In addition to the use of modern navigation equipment and the correct installation of the satellite antenna one uses the telematics server software in the GLONASS / GPS vehicle monitoring system in order to improve accuracy. Such software implements special algorithms for filtering short-term "jumps" of coordinates, statistical processing for more accurate determination of parking locations and data on the quality of the constellation of satellites to determine the probability of error and calculate the corresponding correction value.
When using the GLONASS and GPS satellite monitoring systems in joint receivers, the accuracy of coordinates is always higher due to the large number of visible spacecraft and the optimal relative position. The use of a joint satellite positioning and vehicle monitoring receiver gives an increase in accuracy by an average of 40-60%.
Thus, the use of modern satellite navigation and machinery monitoring systems makes it possible to achieve the highest accuracy and efficiency in calculating the volume of actual production work when performing mechanized agricultural work.